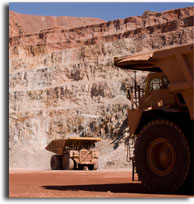
Through continued research and in-field testing, Power Service has developed industry-leading performance additives that improve fuel economy and overall engine performance. Just as diesel fuel and engine technologies continue to evolve, we are constantly improving our additive technology to address the needs of the diesel industry. The unique performance enhancements that Power Service diesel additives provide are the result of a commitment to being the industry leader in diesel additive technology for both new and legacy equipment.
Improving Engine Performance with Diesel Kleen® HPCR Detergent Technology
To realize the benefits of today's cleaner-burning ULSD fuels and advanced High Pressure Common Rail (HPCR) injection systems, new diesel detergent technology is required to maximize performance. In order for HPCR injection systems to efficiently produce more power and reduce emissions, the fuel is stored in a central accumulator rail under extremely high pressure (25,000 to 30,000 psi). The fuel is delivered to each electronically controlled injector to provide up to 6 injection events of atomized fuel per combustion cycle. HPCR injection systems provide significant performance improvements as a result of more specific internal tolerances (2-3 microns) and higher injection pressures.
HPCR diesel injection systems provide quieter, more efficient diesel engine performance, but as with most new technologies, HPCR has created new operational challenges for the diesel engine operator. The operational challenge for HPCR injection systems is Internal Diesel Injector Deposits (IDIDs). These deposits are different and distinct from conventional nozzle deposits. IDIDs are produced primarily in the injector valve seat but can also be found in the nozzle areas of HPCR injectors. They are formed as a result of injector temperatures that exceed 350°F. causing a chemical reaction between corrosion inhibitors and sodium or calcium, commonly found in ULSD at low ppm levels. IDIDs result in a slow response or sticking of moving internal parts, resulting in a loss of injection event timing and variances in the amount of fuel delivered to the cylinder. A slow or sticking injector response causes excess fueling into the cylinder, resulting in increased emissions, decreased fuel economy and excessive power loss.
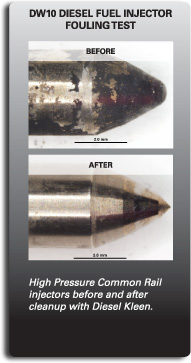
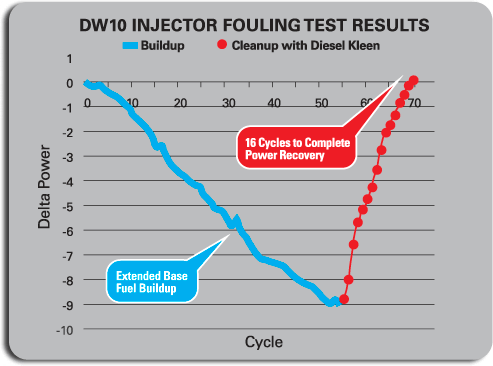
To address IDID formation in HPCR injection systems, an engine test was needed to replicate in-field issues experienced by Original Equipment Manufacturers (OEMs). In March 2008, the CEC (Coordinating European Council) approved the F-98-08 DW10 Injector Fouling Test. The DW10 test uses a Peugeot DW10 2.0-liter, 4-cylinder, direct-injection turbocharged engine that is representative of new future diesel engine design. It directly measures engine power, which is a function of the level of injector fouling.
A high-speed, high-load, one-hour cycle forms the basis of the test. At the beginning of the test, the cycle is run 16 times to break in the fuel injectors. Following this break-in period, the cycle is then repeated over an 8-hour block with an engine power measurement logged at the end of each one-hour cycle. This is followed by a 4-hour "soak" period (engine off). The 8 one-hour cycles followed by the 4-hour soak is repeated two more times followed by a final 8-hour cyclic running period. This gives a total of four 8-hour periods of running and three 4-hour soak periods, which results in 32 hours running time (with 32 corresponding engine power results being logged) and 12 hours total soak time. The total test time for the method is therefore 60 hours (16 + 32 +12).
The DW10 test provides a benchmark for evaluating the effectiveness of injector deposit control additives to both prevent and rapidly remove IDIDs. This new test method has significantly increased the deposit control requirements of diesel detergent in comparison to previous L-10 and CEC XUD-9 test methods.
Power Service Diesel Kleen® Detergent Technology has been tested using the DW10 procedure and proven effective in both preventing and removing IDIDs from HPCR injectors. Diesel Kleen provided complete power recovery losses in the DW10 Diesel Fuel Injector Fouling Test in as few as 16 cycles. Diesel Kleen prevents power loss and eliminates IDID formations to provide diesel engine operators immediate improvements in fuel economy and power that more than pay for the cost of the additive.
Cetane number is a measure of the ignition quality of diesel fuel – the higher the cetane number, the shorter the ignition delay. This high-energy compound improves overall combustion within engine cylinders resulting in quicker engine starts, more power and improved fuel economy.
The Engine Manufacturers Association (EMA) states, "Fuels with low cetane numbers will cause hard starting, rough operation, noise and exhaust smoke. Generally, diesel engines will operate better on fuels with cetane numbers above 50 compared to fuels with cetane numbers of the national average of 46."
Power Service firmly believes in the performance benefits associated with increased cetane, which is why we formulate +Cetane Boost technology in our additive packages. The combination of +Cetane Boost and Diesel Kleen detergent technologies results in overall engine performance that is unequalled by any other diesel additive manufacturer. It provides faster cold starts, quieter engines with more power and improved fuel economy up to 8%.
Modern diesel engines rely on diesel fuel to lubricate fuel injectors and pumps in both HPCR and non-HPCR equipped engines. Without proper lubrication, the components of these systems (which have tolerances of 2-3 microns) are subjected to increased wear and premature failure.
In 2006, the EPA mandated the introduction of Ultra Low Sulfur Diesel (ULSD) which has no more than 15 parts per million (ppm) sulfur. To remove sulfur and aromatics from diesel fuel to meet the EPA specification for ULSD, refiners utilize a process called hydro-treating. Unfortunately, the hydro-treating process also removes many of the nitrogen and polar compounds that provide natural lubricating properties in diesel fuel.
To address this issue, the American Standards for Testing Materials (ASTM) created testing method D6079 which utilizes a High Frequency Reciprocating Rig (HFRR) to measure the lubricity of diesel fuel. ASTM D6079 requires a maximum 520 micron wear scar diameter (WSD) as the minimum lubricity specification for diesel fuel. The Engine Manufacturers Association recommends a minimum WSD specification of 460 microns to protect the fuel pumps and injectors on their engines.
The Technical Services Laboratory at Power Service tests hundreds of diesel fuel samples annually using ASTM D6079. The test results show that 44 percent of all diesel fuels tested fail to meet the ASTM minimum WSD specification of 520 microns and exhibit an average failing WSD of 617 microns.
To address these fuel lubricity challenges, Power Service Products has formulated Slickdiesel Lubricator as a cost-effective technology to protect fuel injectors and pumps. Slickdiesel Lubricator meets or exceeds the ASTM D6079 specification in ULSD fuels and protects fuel pumps and injectors from premature failure.
Fuel Stability and Fuel-Filter Plugging
ULSD fuels degrade more rapidly due to the hydro-treating process used by refineries to remove sulfur. The natural anti-oxidation properties of diesel fuel are decreased as sulfur is removed, causing ULSD to become thermally unstable when exposed to extreme heat.
Temperatures within HPCR injectors can exceed 350°F. which causes thermally unstable ULSD fuels to darken, produce gum residues, form sediments and solid deposits that cause premature fuel-filter plugging and injector sticking in diesel engines.
Thermal instability can also cause the formation of asphaltenes which are naturally occurring organic hydrocarbons found in diesel fuel that contribute positively to the fuel's BTU value. Extreme heat causes asphaltenes to polymerize and come out of suspension, resulting in black soot formations on fuel-filters.
Continuous use of Diesel Kleen prevents the darkening of diesel fuel caused by polymerization of asphaltenes, which agglomerate and plate out as black deposits on fuel-filters, pumps and injectors.
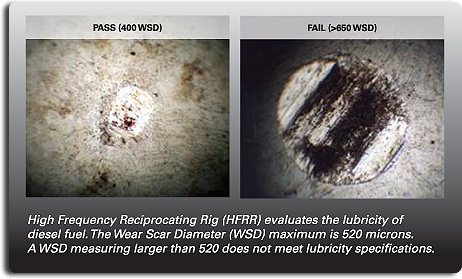
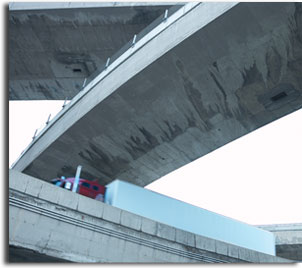